The Japanese Pattern Challenge
A blog born from the desire for a winter coat in a color other than black. With limited sewing experience and no knowledge of Japanese I've worked through all the patterns in Ryuichiro Shimazaki's book on men's coats. If I can do it, anyone can! But the challenges continue. Join me as I continue to explore the world of menswear. I AM my own luxury brand!
Saturday, May 12, 2018
I've moved!
Someday I hope to find a way to automatically redirect viewers to the new blog. But for now you'll just have to click on the link.
Consider following me (I think you'll find a place at the bottom of the main page to sign up). You'll be notified via email when there's a new post.
The new blog is a work in progress, so please be patient. I have a lot to learn about Wordpress!
Thursday, March 1, 2018
Instagram, a first step
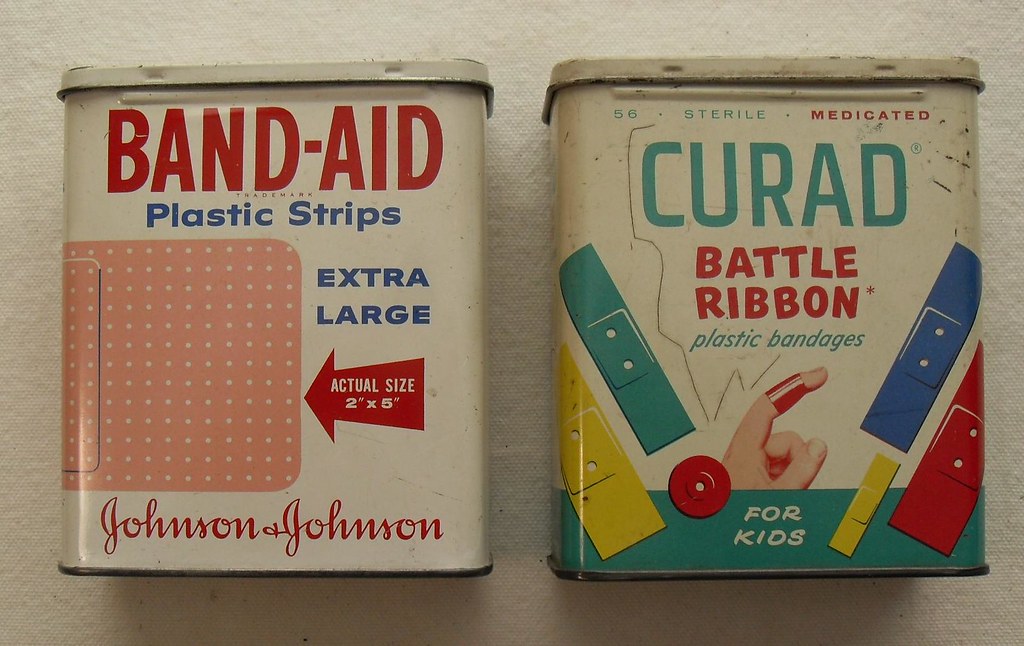
Wednesday, February 28, 2018
Change is in the wind
Sunday, February 25, 2018
Suit progress and... learning some new skills
With the jacket fronts complete I moved on to the sleeves. It was a nice break from all the detail work (pockets, taping and pad stitching). The sleeve construction is really quite simple, it just gets fussy where the lining meets the vents.
A wide strip of pocketing cut on the bias is basted into sleeve cuff. The vents and hem are folded into position and slip stitched into the pocketing.
No stitches are visible from the outside. It's like the hem is held in place by magic!
Getting the lining in around the vents is NOT magic! It took me awhile to figure out what part overlaps what, and how to get from one side to the other. Working with lining material is its own special hell. It's a lot of frustrating work for something that will never be seen!
Moving on.....
Are there any perfect patterns? Hmmmmm. This pattern, as much as I like it, has its issues. The first issue to rear its head turned out to be the jacket front facing (which becomes the lapel when it's folded back). The lapel edge is curved. Why is this a problem? If you're working with a stripe, the stripe will fall off the lapel rather than be parallel to it. My fabric has a subtle striation to it, so the front facing needs to redrafted.
The original pattern piece is on the bottom. Notice the curved edge. The new pattern piece on top is drawn with a straight edge. Using an iron and LOTS of steam, the new facing is curved to match the original pattern piece. Steam is used to shrink the other side of the facing which will ripple up during the process. This is where working with wool is a wonder!
Once this step is accomplished a new front lining will have to be drafted. Usually I make an inside breast pocket that slightly overlaps onto the facing. This is pretty standard stuff on all RTW jackets. But now all my usual pattern pieces are out the window. Arghhhh, what to do?
I turn to Cabrera's "Barcelona" pocket.
Confession..... I can get totally freaked out by sewing illustrations.
Just looking at this scares the sh** out of me! In my head I just assume that this is WAY beyond my ability. I've always skipped over these pages of Cabrera's book, and retreated to familiar territory. But this time I'm pretty much forced to confront it. And guess what?
It's way easier than I ever imagined!
Like so many things in tailoring, it really comes down to careful measuring and taking things one little step at a time. Making the Barcelona was actually less work than the usual double piping pocket that I've used in the past. I'm sold! If you can measure and cut a rectangle, you can make this pocket.
And here is the completed pocket. I did add one extra step....I fused a very lightweight interfacing to the back of the lining. This made it much easier to work with, and I'm all for that.
Working along, the jacket pieces get sewn together and the lining pieces are basted into position. I know this isn't everyone's cup of tea. The combination of basting and having extra wide seam allowances on the lining pieces makes this process much easier. This is the essence of "slow fashion", and it can actually be very satisfying. Using silk thread for the slipstiching makes it go so much easier because it's much less inclined to tangle.
My next issue turned out to be the collar. I've made this jacket a few other times and have fiddled with the pattern piece multiple times. Somehow I've lost the revised pattern, because what I have doesn't come close to fitting the neck opening. GRrrrr. I should take better care of my patterns when I file them away.
Enter more intimidating illustrations!
This takes me back to the nightmare of Algebra II in highschool. I never dreamed that I'd be using this page from Cabrera, but here I am needing to draft a new collar. And guess what..... this was F'ing easier than the Barcelona pocket!!!
I just followed along step by step, and voila! Here is the original pattern piece (white) sitting on top of the new pattern (brown). Any wonder I couldn't get it to fit? Another new skill obtained.
The collar is constructed on a base of French canvas and undercollar felt. It doesn't show in this picture, but a piece of pocketing is sandwiched between the layers at the collar ends to add even additional body.
The whole assembly is pad stitched together in a circular pattern. Because the components are very stiff, it's sort of like pad stitching a cardboard box. Silk thread makes the process easier. After pad stitching the collar it's shaped on a tailor's ham with lots of steam. The result is well worth every bit of effort; and having done it a few times, I wouldn't consider making the collar any other way.
Here is the collar attached to the neckline of the jacket. The newly drafted pattern fit perfectly. This is a good place to stop for now.
Thursday, February 15, 2018
Next up -- Wedding #2
Here we go, another wedding! This time, my beautiful and uber talented daughter is marrying. The place -- Oakland, CA. The date -- April Fool's Day (which also turns out to be Easter this year).
My travel arrangements are all made, but my Father of the Bride wardrobe is sorely lacking. My daughter floated the idea of my wearing my whole Scottish kilt garb, but I think it's way too flashy. I think the bride should be the star of the show, not her crazy old man. Call me old fashioned, but I think a dark (dark-ish) suit is called for.
Enter "La Mer" from Sawyer Brook Fabrics, a heathered / striated 100% wool suiting from Italy. Wow! The quality of this fabric completely exceeds my expectations. I ordered it from a swatch and can't be happier. The yardage I received is flawless, and I absolutely love the color -- a dark teal blue. (Unfortunately my cheap point and shoot camera does a horrible job capturing the color). Sawyer Brook offers a swatch service, which I will most likely subscribe to. Their retail store is in central Massachusetts, about a 3 hour drive for me, and I can easily foresee a field trip in my future.
I prepped the fabric using the London Shrink method. I've done this many times, and it's a safe and reliable way to preshrink wool fabrics. Cotton sheeting is soaked in water and then well wrung out. It's sandwiched into the fold of the material.
Once everything is sandwiched, the fabric can be folded up and wrapped in plastic to set overnight. The moisture from the sheeting is absorbed into the wool to create a uniform dampness. The yardage is then air dried and ironed. This suiting required almost no ironing once it dried. There are benefits to working with high quality fabrics!
I have no access to menswear tailoring supplies here in Maine. Maybe you have the same issue? Fear not, B. Black and Sons to the rescue. They offer a "Jacket Packet" which contains everything you'll need. A pair of premade haircanvas jacket fronts, more than enough lining material (I think you could actually screw up a piece and have enough to recut another!). Sleeve lining, a huge piece of pocketing, collar felt, a strip of French canvas for the collar, shoulder pads and sleeve heads. (The buttons aren't so hot). This packet is my "go to" when a trip to NYC is out of the question.
I'll be using my old standby, this very beat up Bill Blass suit pattern from the early 80's. This is just a nice all around jacket pattern. No crazy lapels, typical menswear pockets, vented sleeves and double back vents. I've only made the trousers once, but they're also straight forward, classic.
I won't go into great detail. The jacket fronts are by far the most work. I use Roberto Cabrera's book on menswear tailoring as my guide. None of it is particularly hard, it just pays to be as accurate as possible, both in measuring as well as sewing. If I'm tired or "just not feeling it" I put everything aside. Things go so much better when I'm fresh, which is usually the next morning.
Another huge benefit is having the right thread to work with. Real cotton basting thread and a spool of silk thread that matches the fabric makes the work go so much faster, and with less aggravation. So much of tailoring is about control. All the basting is about taking control of the fabric and making it conform to the body.
Here are the completed fronts. From here I like to move to the sleeves. They're made fully lined, and there's a fair amount of fussy work around the vents. I HATE working with polyester lining material, so the sooner this part is over the better!
So far, so good. Be well, and enjoy your current sewing projects!
Tuesday, February 6, 2018
Wedding #1, the recap
I realize that I never really wrapped up the kilt project(s). It all got a little overwhelming. Rather than blab on and on about the whole endeavor, I think I'll just let the wedding photographer's blog post illustrate what an extraordinary event two amazing young people, and their loving families, created on a farm in Maine.
http://iamsarahv.com/blog/weddings/william-allen-farm-maine-wedding-photographers-fall/
Having my son ask me to make a kilt (and the whole nine yards) was a huge honor. We're talking real once in a lifetime stuff. If there's anything my sewing journey has taught me, it's that there's value in the "realness" of the clothes that we create. Yes, there may be little mistakes here and there, something that could have turned out better, but in the end what we make is honest. And all those threads....not only the physical ones that are holding things together, but the emotional, spiritual, loving threads we spin, simply can't be had "off the rack".
Credits
Tartan fabric, Strathmore 11.5 oz, "Dress MacLeod". -- Irish Traditions, Annapolis, MD
Wool suiting and linings. -- AK Fabrics, NYC
Tuxedo satin and tailoring supplies. -- B Black and Sons
Pewter Prince Charlie buttons. -- Three Feathers Pewter , Millersburg, OH
Custom dress sporran. -- Artisans of Scotland
Kilt hose, Clan kilt pin and brooch. -- USA Kilts
One final twirl!
Sunday, December 24, 2017
The ?Couture? Jacket -- Wrap-up
Do you remember that I was considering making a "French Couture jacket"? It was ages ago. You've probably forgotten the whole thing. I armed myself with Claire Schaefer's book, cranberry wool tweed woven by my mom, bronze buttons and some foufy mohair trim. So what the hell happened.....where to begin?
The general consensus from you, my readers, was that the froufrou trim had to go. I'm just not Pharrell Williams enough to pull that look off. On me, it would be "ladies who lunch" gone WAY wrong. So I went back to the trim stores in NYC and settled on a burgundy faux suede with contrast edge stitching. Decidedly simpler but not flexible enough to conform to my pattern's curved collar and lower front edges. Rather than fight with the trim to make it curve, something it was NEVER going to do, I squared off the collar and jacket fronts. In sewing, as in life, you have to pick your battles.
Overall, the pattern was fairly easy to fit. I increased the width of the collar (there just wasn't enough room for the trim), shortened the body by about 4" and added extra curve to the upper back (the dowager's hump adjustment, ouch! Like that doesn't make me feel ancient). Then the real games began.
Straight up....if you're looking for the most complicated and time consuming way to construct a garment, this "Couture jacket" will be right up your alley. None of it is particularly difficult....cumbersome is the word that comes to mind. Here I'm cutting off all the pattern seam allowances to start.
Then the pattern shapes are thread traced onto the fabric. There is, of course, a very specific way in which this is done. Thankfully, Schaefer's book is well illustrated. The grain line, notches and any other marks are also marked with thread. Get ready to use a huge amount of cotton basting thread!
Each thread traced piece is on a rectangle of fabric. I swear, the real "luxury" of this construction method is the shear waste of precious fabric that ensues. The fabric gets handled extensively, so I ran all the cut edges through my serger to prevent raveling.
This is about as far as I got sticking to Claire Schaefer's directions. I started to veer off on my own course... more tailored jacket, less floppy cardigan.
I'm sure Coco rolled over in her grave on this one. I interfaced my jacket fronts with a lightweight hair canvas. The "couture jacket" has just the tiniest strip of silk organza selvedge caught in the front edge openings. I also stabilized the shoulder seam with a semi-bias strip of lining material. That's a Roberto Cabrera thing.
Veering even further of course, I wanted welt pockets and bound buttonholes. Not the patch pockets and handworked buttonholes that are the hallmarks of the couture jacket. Oh, and that "Coco-ism". -- "No button without a buttonhole". Forget that!
I don't know about you, but I always like to practice the tricky bits before I launch into something that has the potential of ruining a project. So....
This is a mock up welt pocket that I made with left over scraps. I used Edna Bishop's method. She calls it a "regulation welt pocket". It's surprisingly simple and straightforward once you get up the nerve to start slashing your fabric! For this jacket, I needed to prove to myself that it was going to be possible, considering the bulk of the fabric. I tried to reduce bulk in every way possible.
As luck would have it, making the pocket was entirely possible. The welt is lined with silk charmeuse to reduce its thickness, and there's some serging that will never be visible to keep some seams flatter. So the welt pockets are a go.
I also made a trial bound buttonhole. The welt is the reverse side of my silk charmeuse beefed up with a scrap of Fashion Sewing Supply's Pro-weft Supreme fusible. Reassured that these features are indeed possible, it was full steam ahead.
A piece of silk organza was used as a reinforcement for the welt opening.
The pocket in process. I baste a lot! But it's always time well spent.
Here is the finished pocket (a success) , and the beginning of a MAJOR screw-up. Maybe you see it. I positioned the welt for the second buttonhole on the WRONG side of the jacket. I blissfully followed Laura Mae's fabulous bound buttonhole tutorial (here), marked, stitched, cut open and flipped everything to the....
WTF have I done moment!!!!
Once my blood pressure was back under control, I set about correcting the mess I'd made. I positioned a new welt piece onto the outside of the jacket (where it should have been in the first place) and restitched everything directly over my original stitching. I then very carefully cut the incorrect welt away as close to the stitching as I could get. With tweezers I was able to remove any remaining fibers. Disaster averted. The buttonhole may be a touch smaller than the rest, but I don't think anyone else would notice. Fortunately, there were no other screw ups.
Arcane construction becomes the norm. Mon Dieu! I quite honestly can't remember how I attached the sleeves, but somehow it happened.
But I've blabbed on long enough. If you've stayed with me this far, scroll down through more "in process" pics to see the final result.
I wore this outfit to host a rehearsal dinner for my son's wedding in October. By then, all the complexities and frustrations of constructing the jacket were a thing of the past, and I just enjoyed wearing it. It truly turned out to be exactly what I wanted. My idea, my execution. A way to honor my mom's artistry and craftsmanship. A little bit French inspired (without the "Ladies Who Lunch" vibe), a little military, a little tyrolian, tailored (but not overly), with a hard to describe sensation of wearing something truly special.
As always, I am so grateful for the support and inspiration I receive from the sewing community. I've sort of fallen off the blog bandwagon a bit, but I still have projects to share. Be well, and happy sewing!