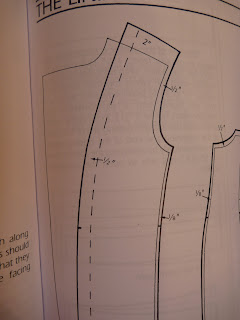
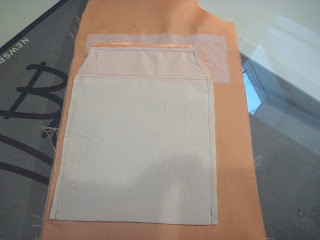
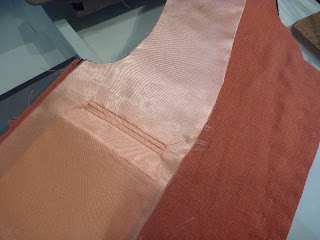
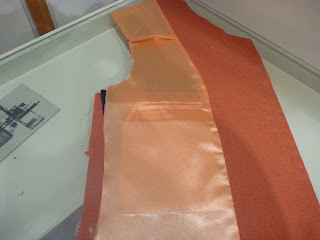
I'm sure no one is crazy enough to be sewing along with me, but if you have the Cabrera book there is a huge error (or at least an area of potential confusion) on page 117! BEWARE!
This is the beginning page of "The Lining". Of course he has you toss out any patterns you might have and start from square one. Using the existing back, side and front pattern pieces one adds extra fabric pretty much all around. The glitch comes with the front lining piece which must overlap the front facing. The illustration indicates just the 1/2" overlap. To make this happen, however, one must add at least an extra inch. In fact, there's no reason to add even more and then trim off the excess at the sides and armscye.
Alas, I added only 1/2". To make things even worse, I put in a double piping chest pocket, which probably took at least an hour to make. In the end the whole mess was too small. There was no room for a seam allowance at the side seam.
Back to the drawing board after considerable swearing. Oh, and did I mention how much I hate working with poly acetate lining material.